Creating a Safer Work Environment: Lessons from National Safety Month 2023
With National Safety Month behind us, it’s time to reflect on some of the valuable insights we gained in 2023. This year’s Safety Month centered around emergency preparedness, slips, trips and falls, heat-related illness, and hazard recognition.
These themes directly resonate with the critical safety concerns faced by organizations in the manufacturing and process industries. And when it comes to addressing these challenges head-on, TenForce’s EHSQ (Environment, Health, Safety, and Quality) software is a vital ally, ready to take center stage.
Let’s delve into the valuable insights we have gained this month and discover how TenForce’s software can provide year-round support for your safety initiatives.
Emergency Preparedness: Creating an Effective Plan
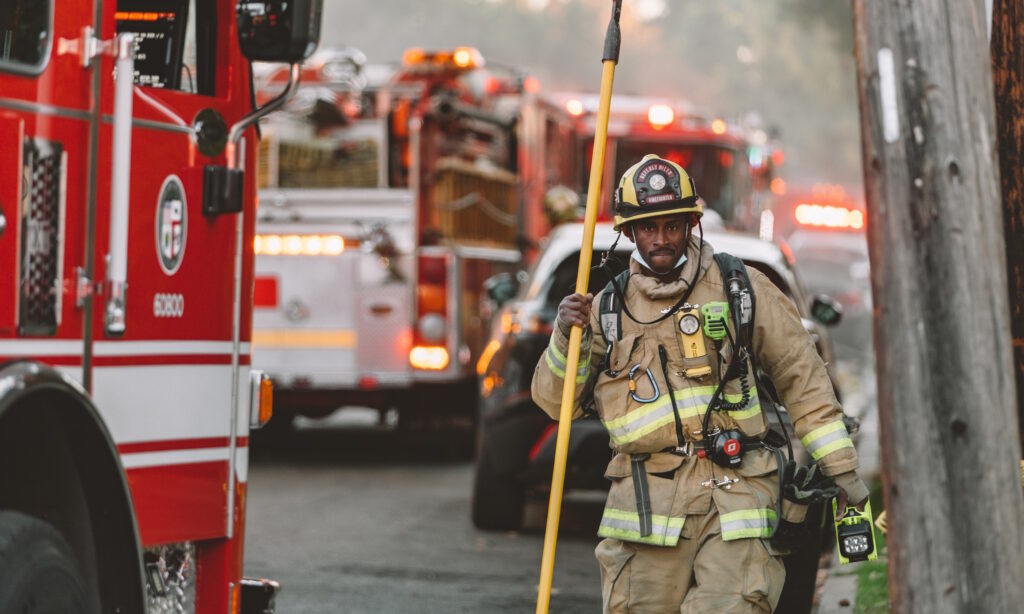
Emergencies like chemical leaks, fires, and explosions can occur without warning, emphasizing the need for prepared and prompt responses. Having a clear understanding of emergency protocols and making thorough preparations ensures that both employers and workers possess the necessary tools and knowledge to safeguard themselves during such critical situations.
When building an Emergency Preparedness and Response program, here are some top tips to consider:
- Conduct a thorough risk assessment to identify workplace hazards considering location, weather, equipment, materials, and processes.
- Develop and communicate clear emergency response plans to employees, including evacuation routes, assembly points, emergency contacts, and designated responsibilities.
- Regularly train employees and conduct drills to ensure effective crisis response.
- Establish reliable communication systems for quick dissemination of information to all employees.
- Maintain essential emergency supplies like first aid kits, fire extinguishers, flashlights, and backup power sources.
- Utilize local emergency services’ expertise and collaborate with neighboring businesses when creating an Emergency Response Plan.
- Develop business continuity plans, identify critical functions and resources, and regularly test backup systems.
- Conduct thorough post-emergency investigations to identify root causes and areas for improvement and incorporate lessons into training programs.
- Regularly review and update emergency preparedness plans to address evolving risks and challenges.
With TenForce you can manage essential components of an Emergency Preparedness and Response Program, including risk assessment, incident investigation, and maintaining up-to-date worker training.
Slips, Trips, and Falls: Mitigating Common Workplace Accidents
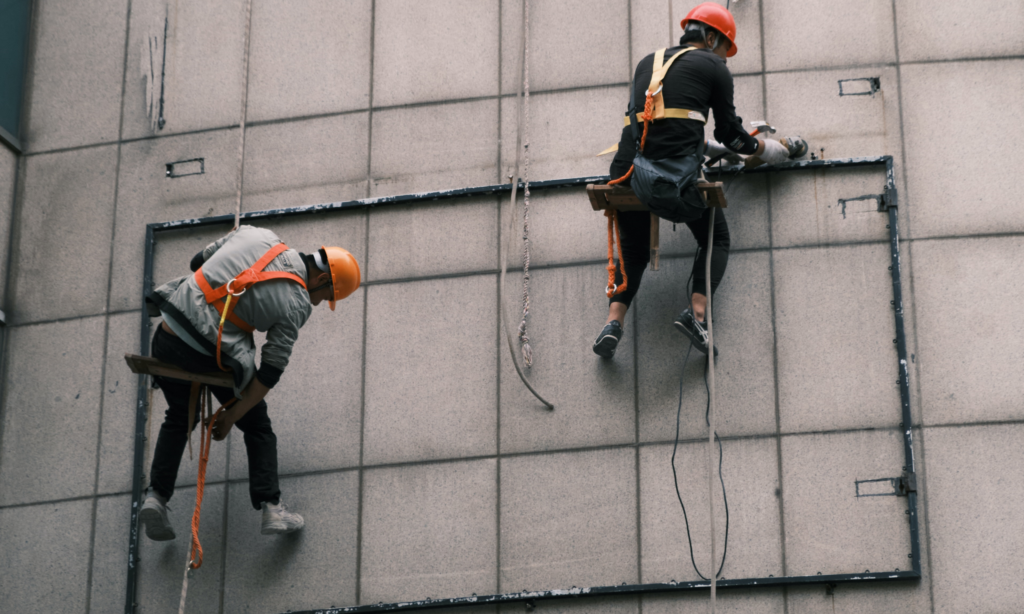
In industrial settings, slips, trips, and falls present substantial risks, leading to injuries and decreased productivity. These risks are amplified by factors like greasy or slippery surfaces, uneven walking surfaces, clutter and obstacles, height differences, the fast-paced work environment, and physical demands on workers.
Proper safety measures, including regular inspections, maintenance, effective housekeeping, hazard awareness training, fall protection plans, and the use of fall protection equipment and Personal Protective Equipment (PPE) are essential to mitigate these risks.
TenForce’s EHSQ software provides a range of tools to mitigate slips, trips, and falls including:
- Our incident reporting and tracking capabilities help you identify high-risk areas, implement preventive measures, and monitor the progress of ongoing safety initiatives.
- Our Permit to Work module ensures that individuals working at heights possess the required training and are well-versed in the necessary safety protocols.
- Our Competence Management Module helps keep workers up to date with relevant training, ensuring their knowledge and practices remain in line with industry standards.
Heat-Related Illness: Ensuring Employee Wellbeing
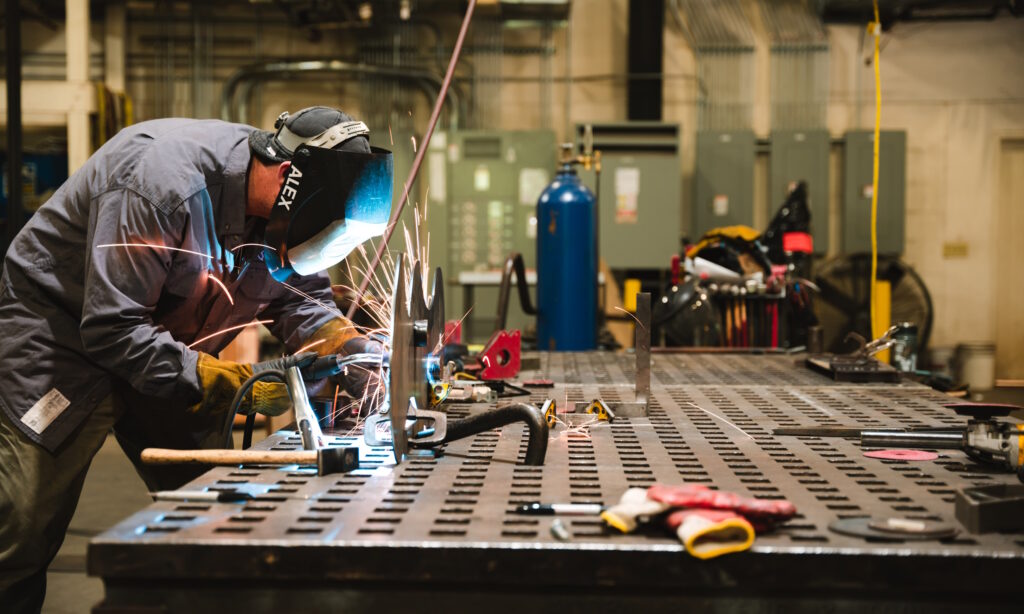
Heat-related illness, such as heat exhaustion and heatstroke, occurs when the body struggles to regulate its temperature due to excessive heat exposure. It is common in manufacturing and industrial environments due to high working temperatures, physical exertion, limited ventilation, protective clothing and equipment, and work environment challenges.
Preventive measures, training, and strategies are crucial to mitigate heat exposure in these workplaces. Manufacturing plants should take the following steps to reduce the risk of heat-related illness:
- Assess heat stress factors: monitor temperature, humidity, radiant heat, workload, and PPE requirements.
- Apply engineering controls: improve ventilation or install cooling systems to minimize heat exposure.
- Implement administrative controls: adjust work-rest schedules, provide breaks, and rotate workers between hot and cooler tasks.
- Establish effective hydration programs: ensure access to cool drinking water.
- Provide suitable PPE: lightweight, breathable clothing, cooling vests, and headgear.
- Conduct regular training: educate workers on heat-related illnesses, prevention, and response.
- Develop an emergency plan: address heat-related emergencies, including procedures for heat exhaustion and heatstroke.
- Regularly review prevention measures: analyze incident reports and near misses and adjust safety protocols.
With TenForce’s EHSQ software, you can take a proactive approach to mitigate heat-related illnesses. Documenting and reporting heat-related incidents, near misses, and corrective actions, will assist you in identifying trends and high-risk areas, enabling you to implement targeted interventions for improved safety. You can also track your training program, building awareness of heat illness and fostering a safer work environment.
Hazard Recognition: Identifying and Controlling Potential Risks
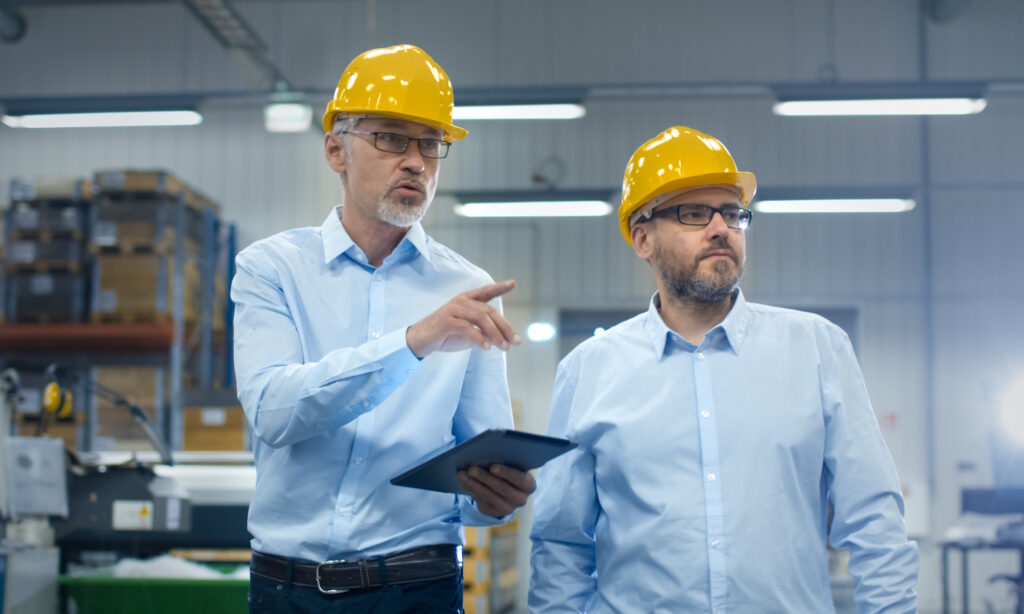
Recognizing hazards in the workplace is the first crucial step toward preventing injuries and fatalities. Hazards, potential sources of harm, pose significant risks to workers’ safety and wellbeing if not identified and addressed.
Hazards can be found throughout manufacturing and industrial environments. They can be physical (e.g., machinery, chemicals, noise, heavy lifting) or environmental (e.g., extreme temperatures, confined spaces, electrical risks). Hazard recognition is vital for process safety management and involves active identification, assessment, inspections, risk assessments, and monitoring.
You can rely on TenForce’s EHSQ software to identify and control potential hazards. With features like risk assessments, inspections, audits, and CAPA (Corrective And Preventive Actions) management, our software allows you to systematically evaluate your work environments, identify potential risks, and implement necessary controls.
Fostering a culture of hazard recognition through comprehensive training and promoting awareness will empower your employees to contribute to ongoing safety efforts. By acknowledging hazards and working towards their identification and mitigation, you can create a safer environment, prevent injuries, and protect your most valuable asset— your employees.
Beyond Safety Month: An Ongoing Journey
As National Safety Month concludes, it serves as a reminder that safety should remain a top priority throughout the year. TenForce is dedicated to supporting your safety efforts, not only in the areas highlighted during Safety Month but also in the numerous other areas of safety. By leveraging TenForce’s EHSQ software, you can enhance safety practices, improve compliance, and foster a culture of proactive risk management. Remember, safety is an ongoing journey, and TenForce is here to accompany you every step of the way!