FrieslandCampina: Using Technology to Streamline the CAPA Process Across the World
There’s no room for improvisation in the food production industry. You don’t need Murphy’s Law to imagine everything that can go wrong in the complex processes and the dreary consequences for public health and corporate reputation.
FrieslandCampina knows all about these challenges. How does one of the world’s largest dairy companies assure the quality and safety of the food chain from grass to glass in more than 100 countries?
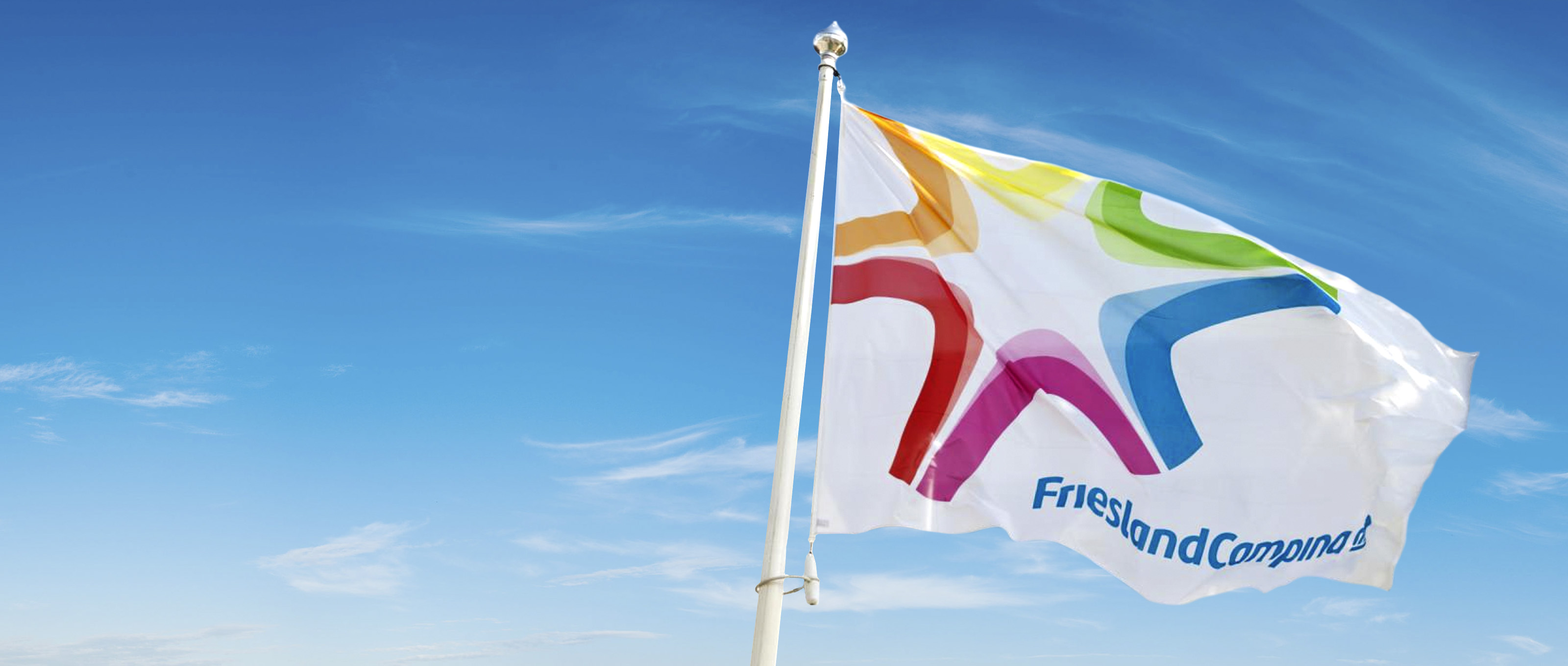
A multinational built on milk
With roots going back to 1879, the Dutch dairy cooperative FrieslandCampina is entitled to add the epitheton ‘Royal’ to its corporate name – as is tradition in The Netherlands. In its home country alone, Zuivelcoöperatieve FrieslandCampina U.A. (which fully owns FrieslandCampina) unites all 16.000 dairy farmers, which is unique. The company is active in 34 countries and has 23.675 employees. The products are sold in more than 100 countries.
Chances are you know lots of FrieslandCampina’s consumer brands, e.g. Fristi, Chocomel, Optimel. But there’s much more. The dairy cooperative also produces ingredients for food companies and has brands for professional customers such as chefs, bakers and caterers. This broad scope of products, all based on the nutrients of milk, is reflected in four business groups:
- Consumer Dairy (milk, yoghurt, condensed milk, cheese, butter, cream, etc.)
- Specialized Nutrition (science-based specific nutrients for infants, elderly, athletes, etc.)
- Ingredients (dairy and plant-based solutions for food, beverage, pharmaceutical and feed industries)
- Dairy Essentials (high-quality cheese, butter and milk powder)
In a Nutshell
Friesland Campina is always looking to be one step ahead of the ever-increasing demands in quality assurance, specific to the food production sector. This time, they were looking for a solution to standardize their QA process around the world. The company chose TenForce to implement a standard CAPA module not only in the European sites but also in Asia. Later, the Document Management and Management of Change modules followed naturally in the process. Now employees from all levels in the company use the modules on a day to day basis, enjoying the benefits of a clear overview over what needs to be dealt with first.
Now employees from all levels in the company use the modules on a day to day basis, enjoying the benefits of a clear overview over what needs to be dealt with first.
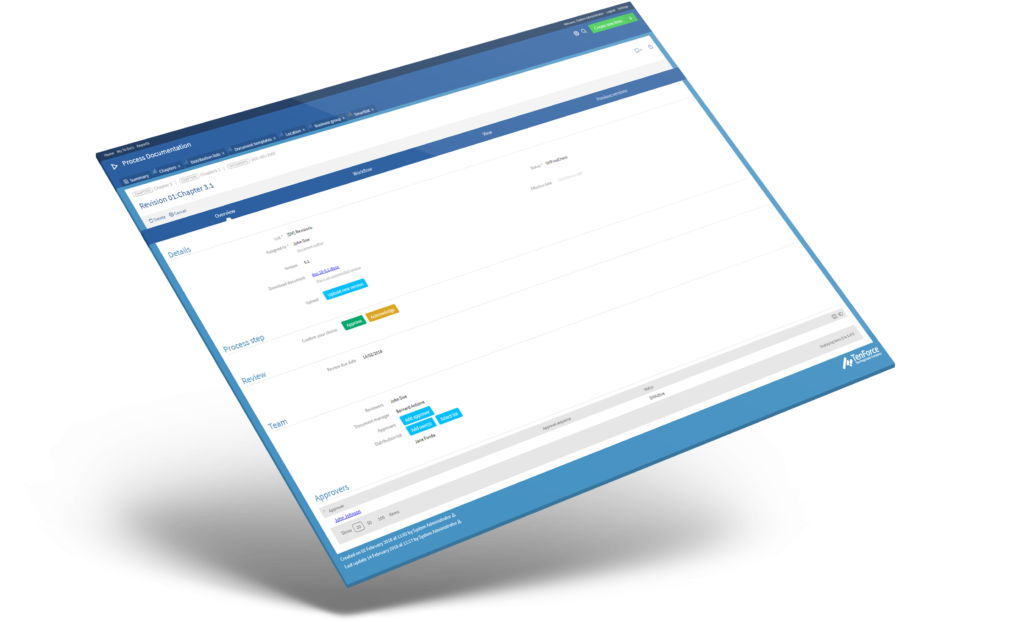
Ensuring Quality and Consumer Safety In the World of Faster, Better, More…
Customers increasingly expect products to be innovative and of the highest standards. For the food production industry in general, coping with a more demanding market and staying competitive while assuring quality, is stressful – and that’s a tremendous understatement.
If mistakes are made, public health may be a serious issue and the reputation of the producer is at stake. Managing health, safety, and environment (HSE) is of the utmost importance.
Organizations tackle these risks by using long-established procedures like Corrective Actions and Preventive Actions or in short CAPA. These are a set of actions required in manufacturing, documentation, procedures, and systems in order to continuously improve the organization’s processes and eliminate non-performance and undesirable situations.
For those unfamiliar with CAPA: you’ll probably have heard of the rigorous Seveso-measures that safeguard the chemical industry. Not meeting the norms, means closure. Same is true in the food production industry, where CAPA is a required part of the quality assurance (QA).
Of course, FrieslandCampina has always put a tremendous effort in all business groups in every country to abide by CAPA. But not in a standardized way. Without centralized tools, every production site had its own way of managing QA and CAPA. An outdated modus operandi that was very labor-intensive and left too much room for all kinds of errors. Hence, FrieslandCampina was at times lacking a clear overview of what needs to be dealt with first.
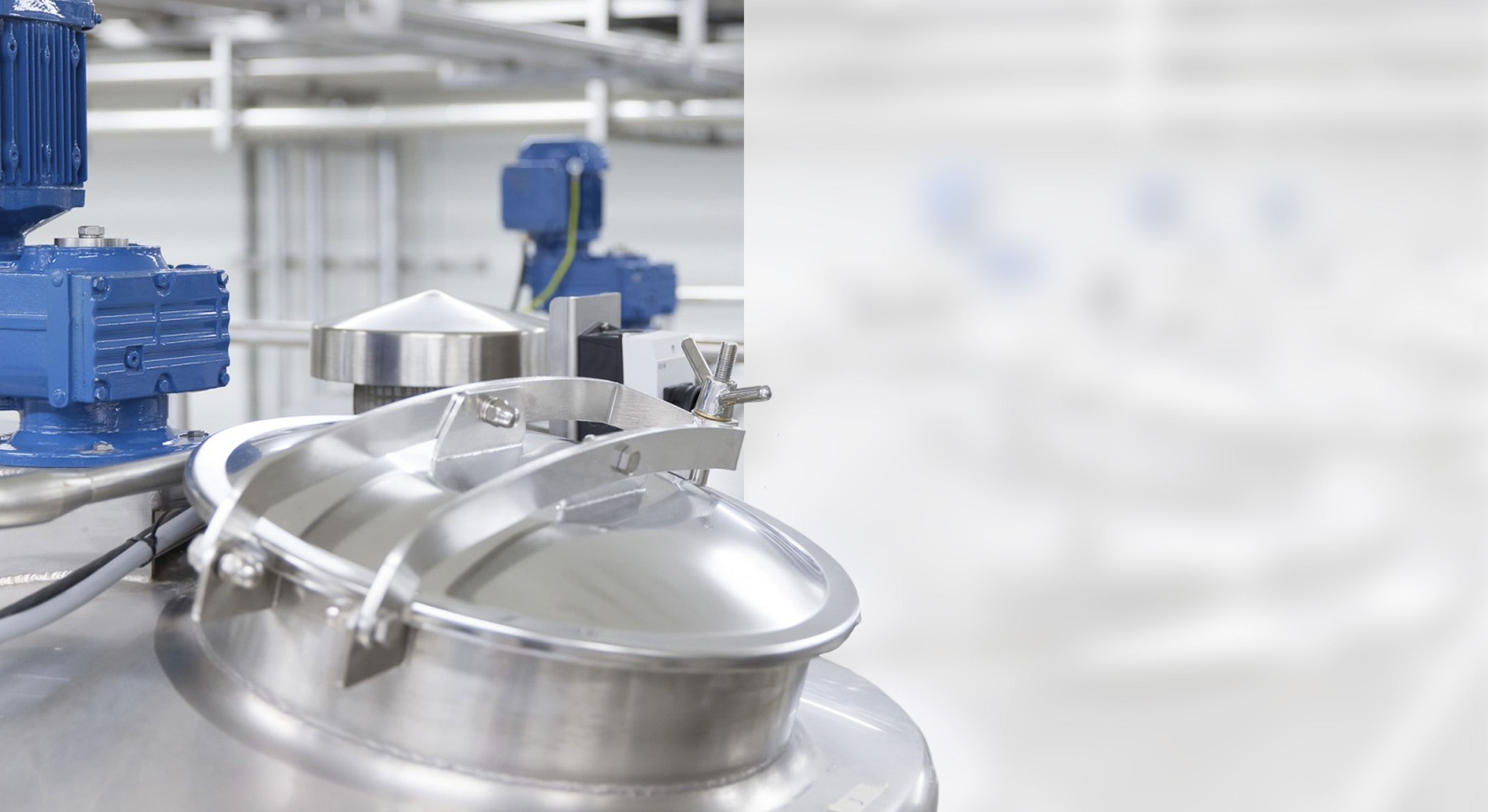
Adopting a Digital Enterprise-Wide System to Manage CAPAs Around The World
At TenForce we share a belief, no, call it an insight: if a challenge is complex, needs to be fed with lots of data and has to be done quick, the solution is called ‘software’. This is exactly what FrieslandCampina needed.
TenForce provided a standard CAPA module to the dairy multinational, which implemented it on a massive scale. Not only in the European sites, but also in Asia. Therefore, TenForce enters a brand-new market with installations in Vietnam, Indonesia, Malaysia, Thailand, Philippines, Pakistan, Singapore, Hong Kong and Myanmar.
The sun never sets for TenForce at FrieslandCampina.
BASTIAAN DEBLIECK
CHIEF COMMERCIAL OFFICER
On top of the geographical mark that has been made, this project is in another way a scoop because for the first time the implementation was done by a third party, Bluecrux, evidencing the TenForce software is highly accessible and easy to manage.
Besides the CAPA module, TenForce also provided Document Management and Change Management to FrieslandCampina. Both modules eliminate improvisation by streamlining and standardizing different processes.