EHS & Operational Risk Management Software
The tool for plant managers and their teams to mitigate risk without sacrificing efficiency.
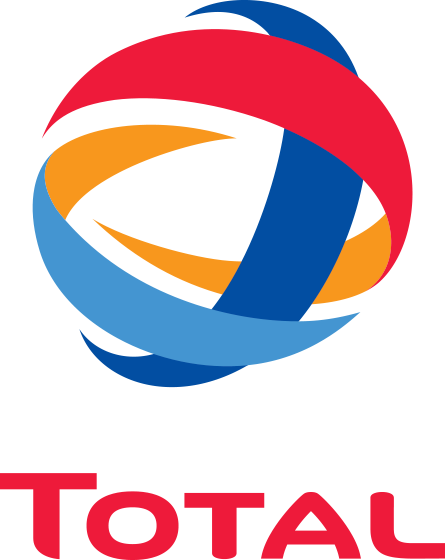
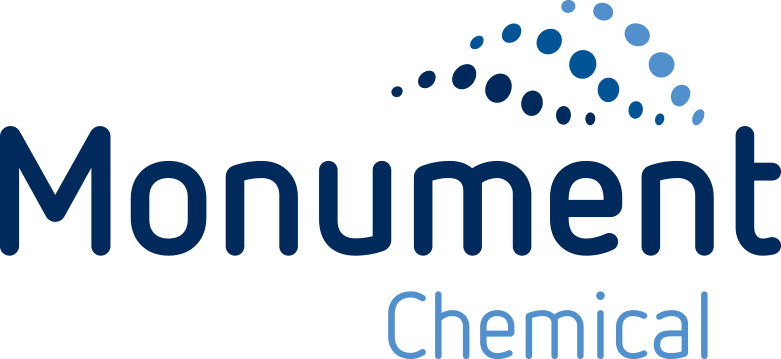

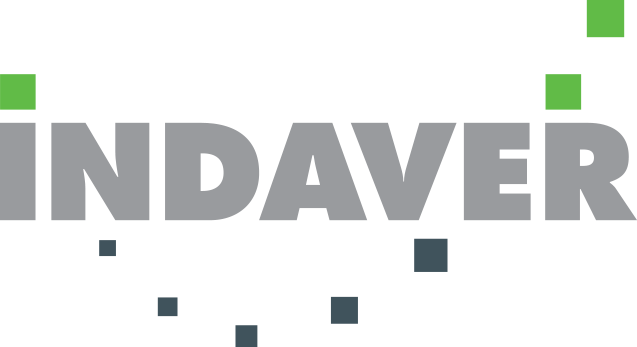
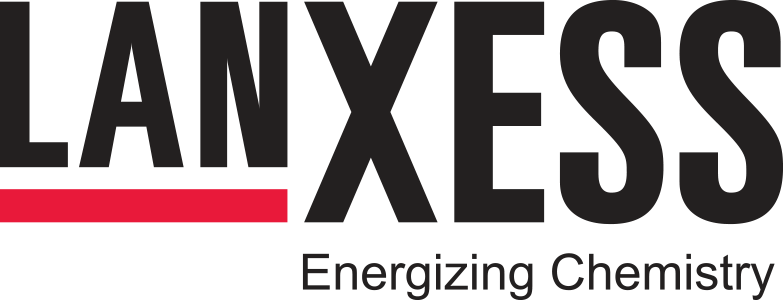
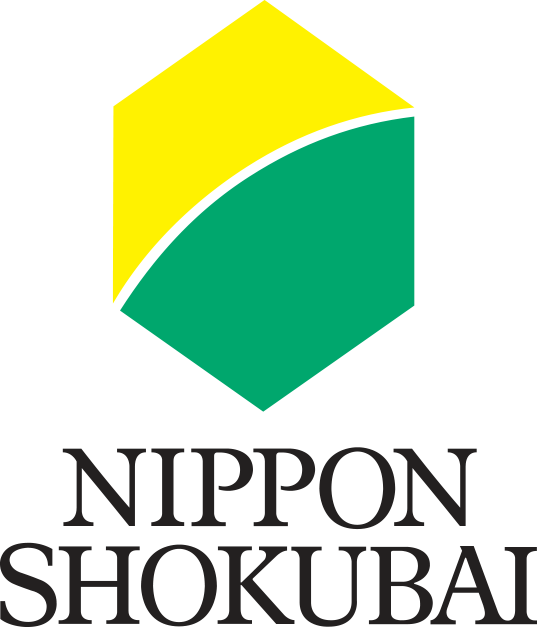

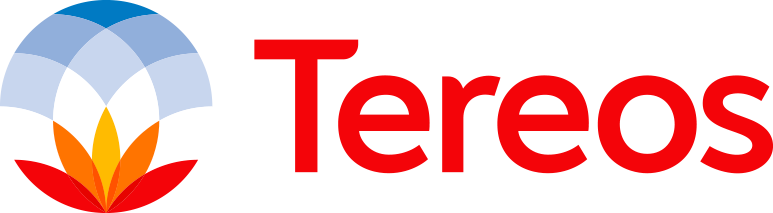
With the average manufacturing site running countless processes, using many different applications, it is a tremendous challenge to make data accessible and actionable. Complying with safety, quality and environmental regulations is increasingly important, but has become more difficult as operations grow.

Choose what’s right for you
Starter Pack
Ideal for corporate teams focused on better managing EHS and ORM processes. Start small and add modules, sites or users as you grow.
Take advantage of more than 10 years of lessons learned, integrated into off-the-shelf, user-friendly solutions. Go for a quickstart based upon best practices, compliant with international standards.
Custom Configuration
Ideal for corporate teams an enterprises looking for international, cross-site, fully integrated process improvements.
Exploit the full capabilities of our platform, and integrate it into your process and application landscape. Go for a tailored configuration, customized to your company needs and processes.
Tenforce Mobile
Outstanding Mobile Experience and Workforce Engagement
Manufacturing companies use TenForce Mobile to make sure operations run smoothly, safely, and efficiently even when tasks need to be performed remotely, on-the-go, or in no-connectivity areas.


Perfectly integrated with the web-based solution, the TenForce native mobile app puts unique features literally at your fingertips:
Join some of the world’s leading corporations in streamlining process safety management while improving mission-critical performance indicators.


Monument Chemical Automates EHS Management, Secures Incident-Free Track Record
As a result of their continuous growth, flexibility demanded by the market and ever increasing regulations, Monument Chemical ramped up their business strategy to standardize and centralize their operations across the globe. The aim was to increase transparency, improve stakeholder accountability and share learned lessons. Read more


Indaver Quickly Registers and Effectively Prevents Incidents with TenForce
Indaver’s activity is very complex because it has to take into account all the different laws and customs from every operation site. As a European organization that navigates the complex and ever-changing waste management environment, Indaver must address incidents efficiently and manage risks proactively. Read more


LANXESS Goes for Full Upgrade of their Process Safety Management Systems
The core business of LANXESS is the development, manufacturing and marketing of plastics, rubber, intermediates and specialty chemicals. Their Antwerp based chemical plants specialize in rubber and glass fibre.
After the success of the TenForce Incidents module, LANXESS decided to move forward with the expansion of their Safety Management practice. Today, four modules (Incidents, Audits, Permits & Isolation and Management of Change) have been fully integrated into their daily operational systems ensuring complete safety and allowing 880 users across two sites to have full access to the necessary tools.


Inovyn Efficiently Mitigates Risks and Manages Changes with Automated EHS Workflows and Processes
Inovyn was seeking a solution that could ensure workers’ safety, efficient action and incident tracking, and compliance with legislation. They also needed a suitable system to manage changes following a structured method and a well-defined process.
After having decided internally what the common processes and workflows for the organisation were, Inovyn decided to adopt the TenForce Incidents Management and Action Management modules. The Management of Change module was later integrated naturally into the system. Inovyn’s stakeholders and our specialists worked together to customize the platform based on the client’s needs. Now employees from all hierarchical levels in the company use the modules on a day to day basis, enjoying the benefits of a modern scalable EHS platform.
Let’s start a conversation today.
+32 (0)16 31 48 60

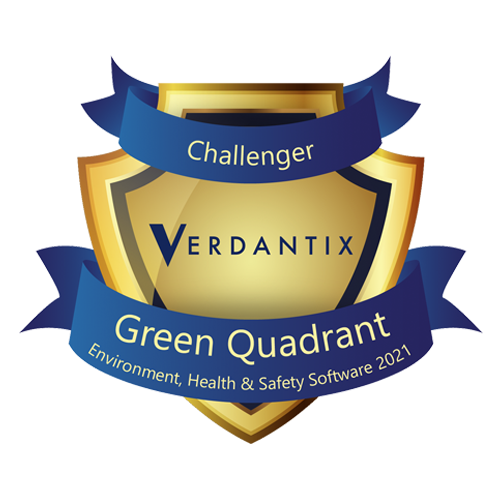
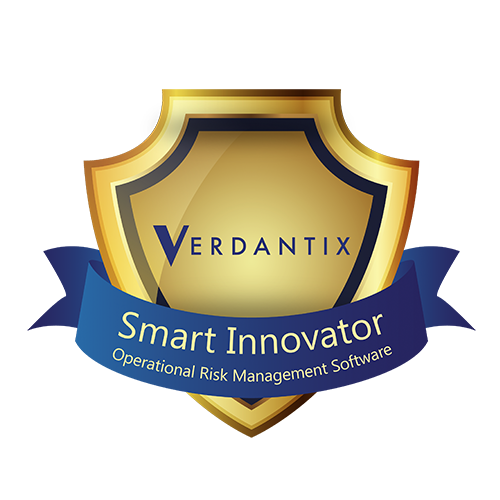
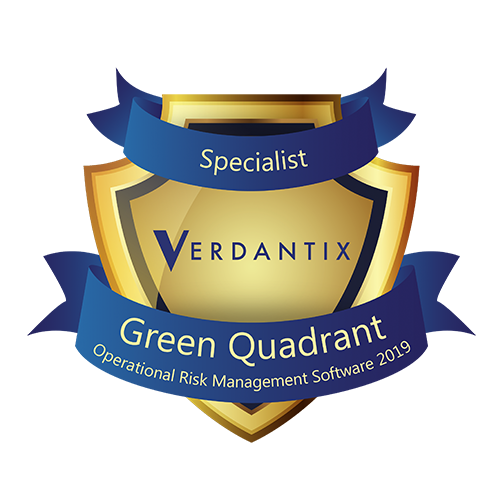
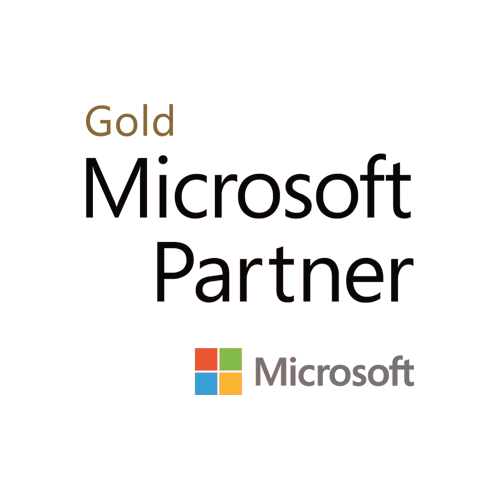
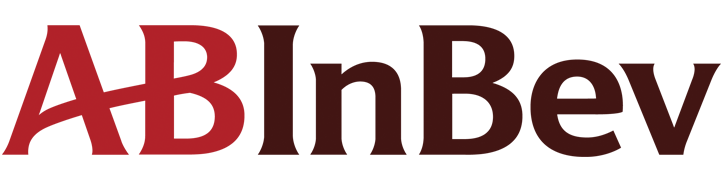
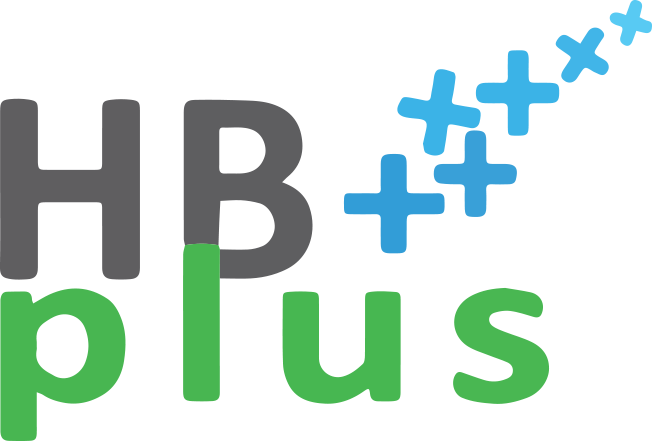
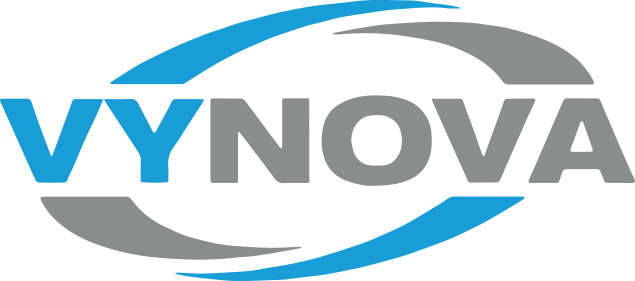
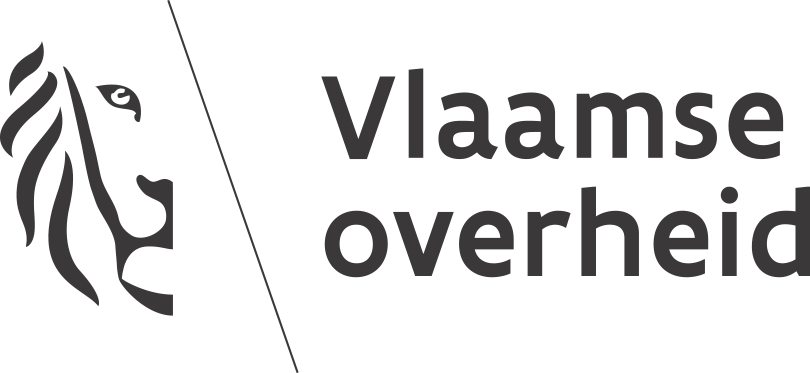
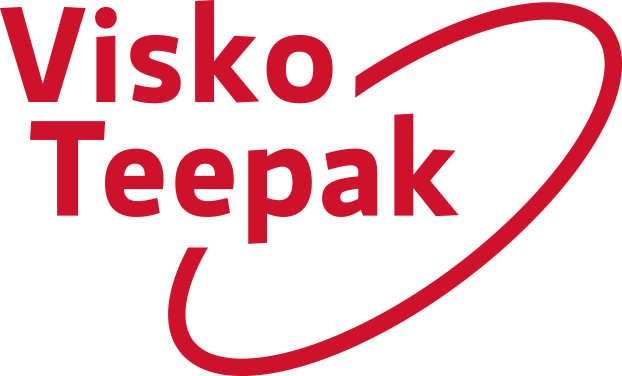
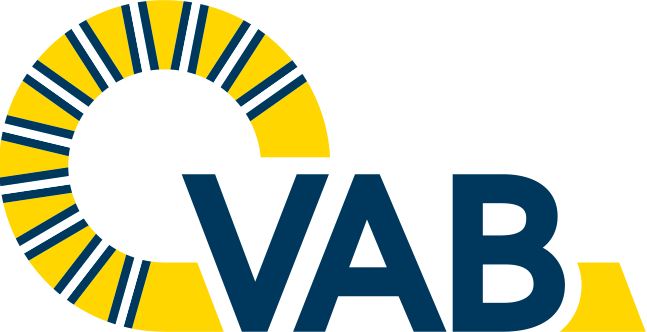
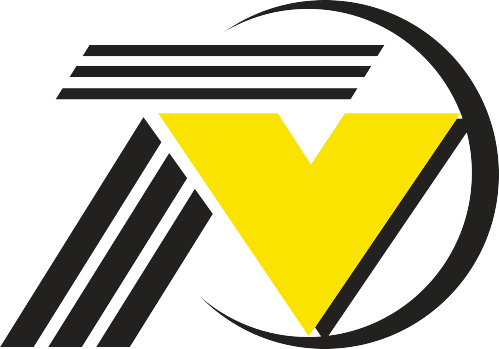

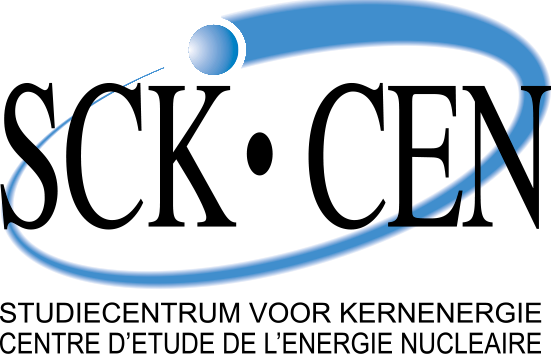

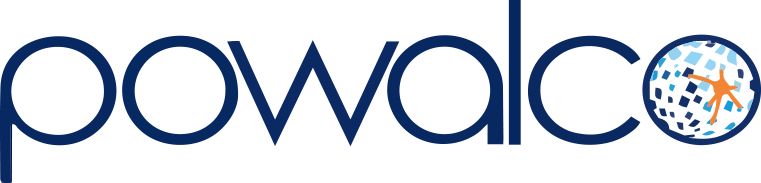
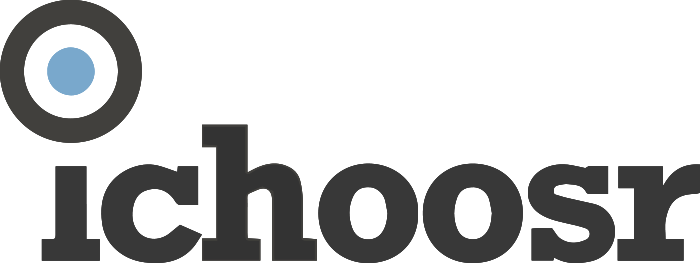
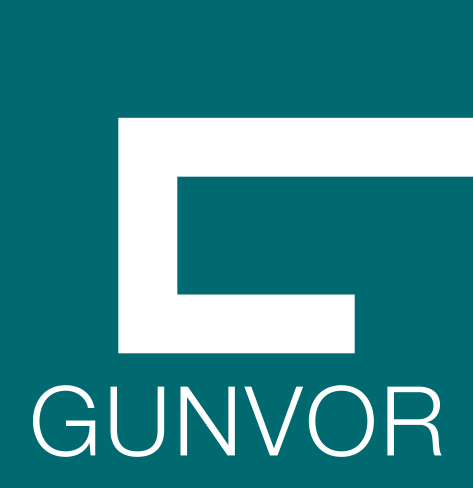
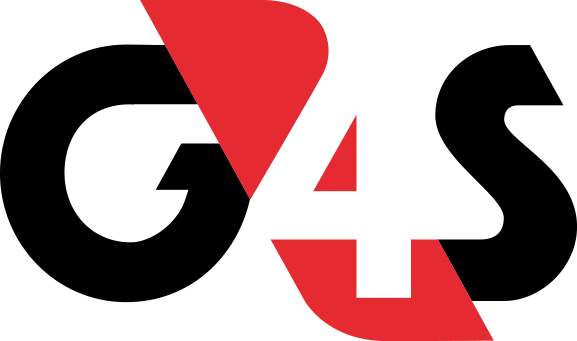
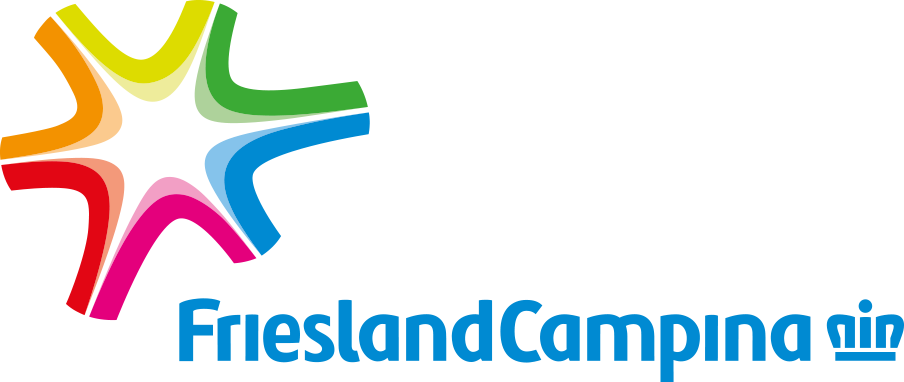
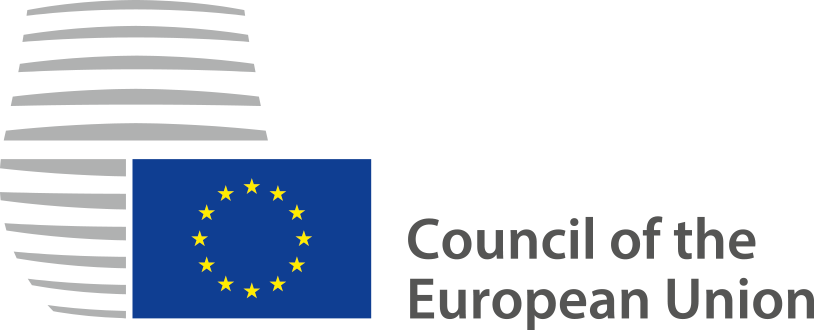
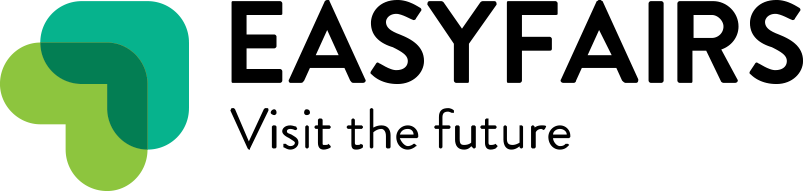
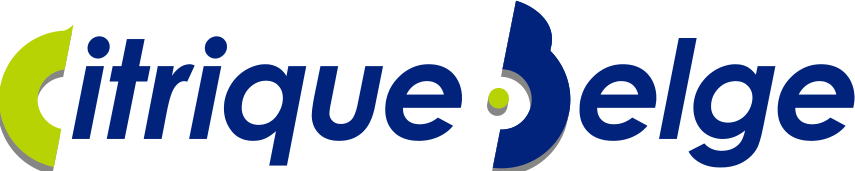


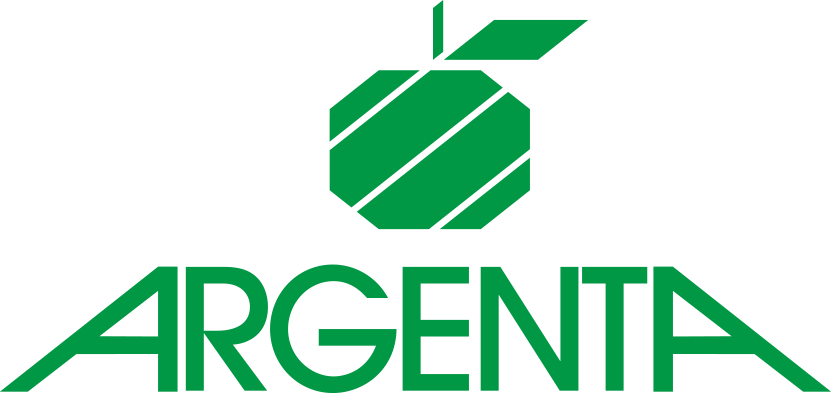
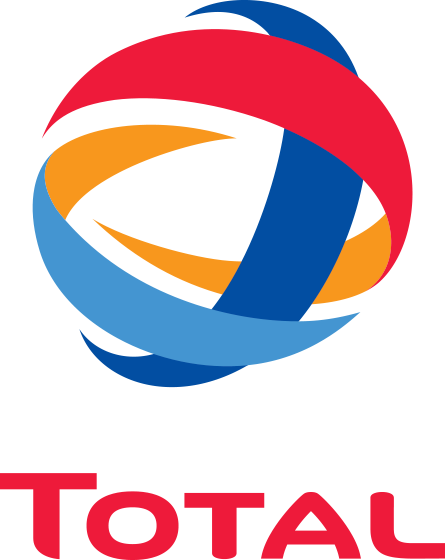
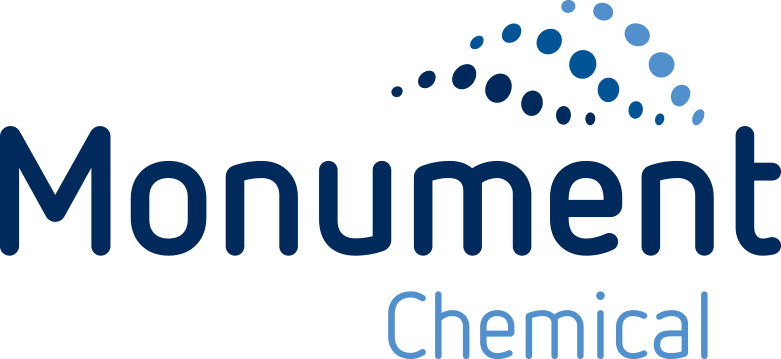


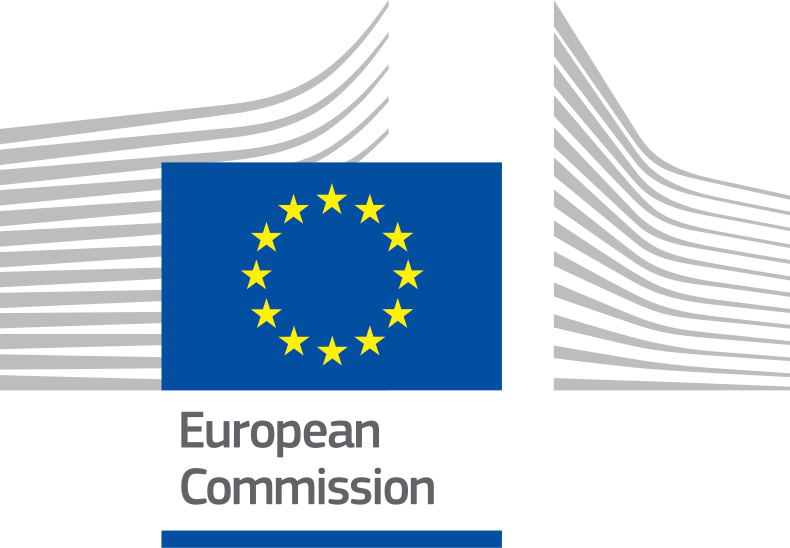
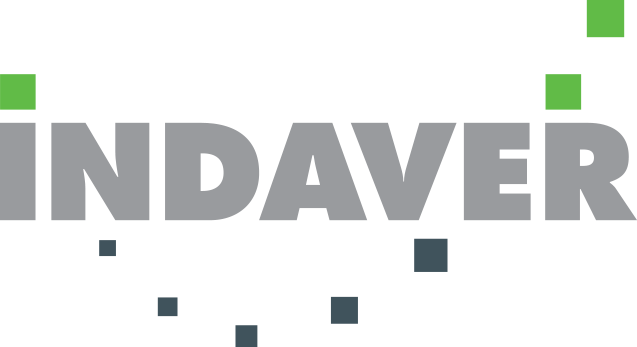


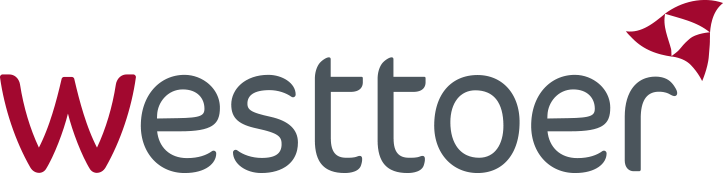
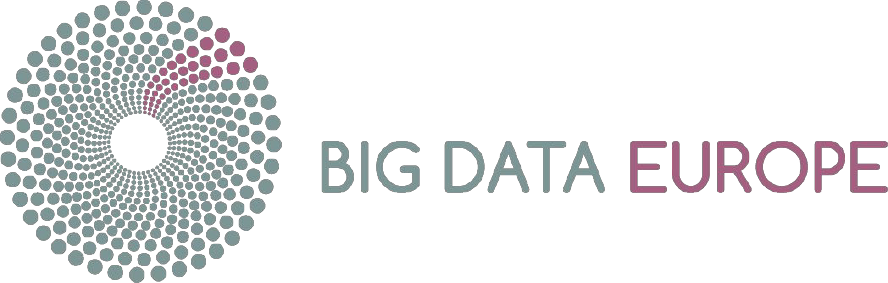

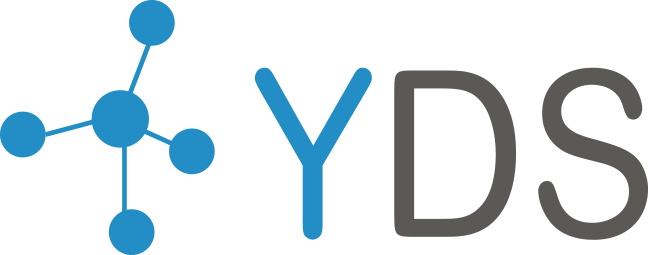
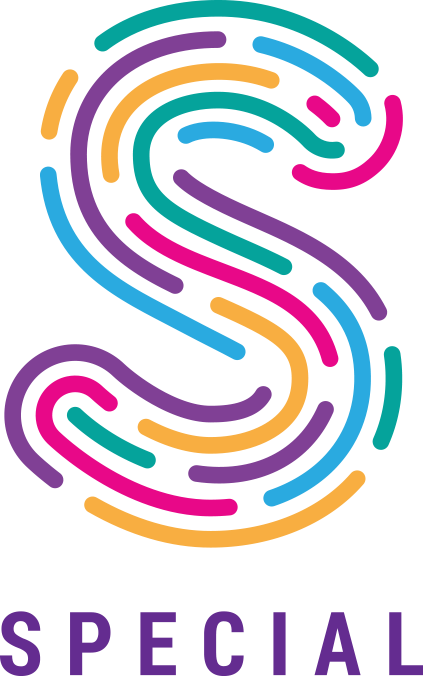
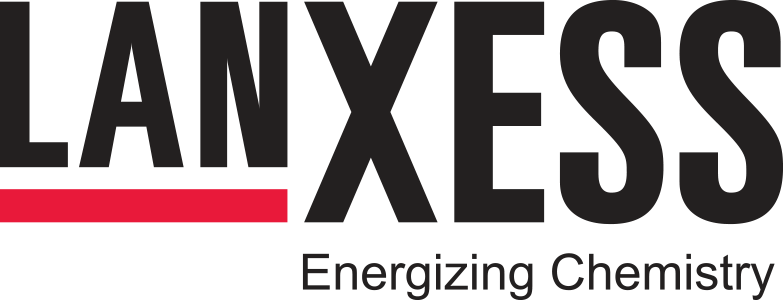
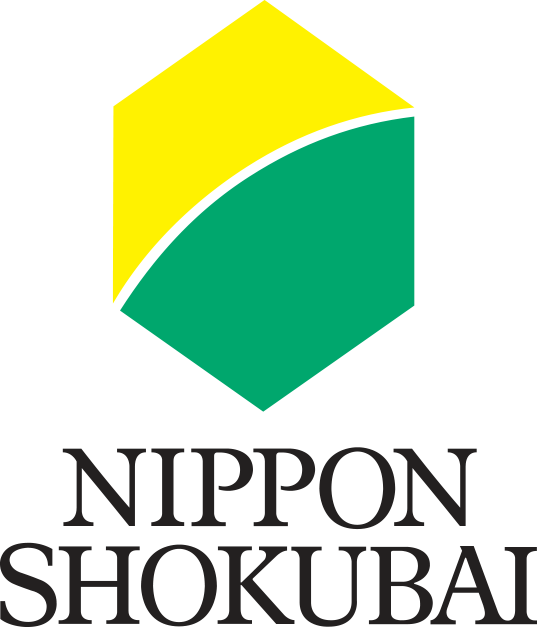
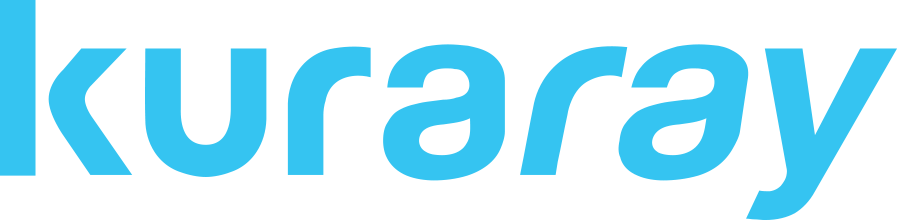

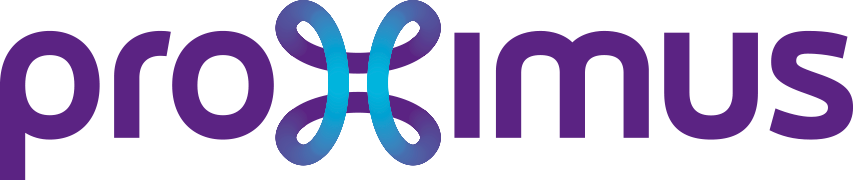
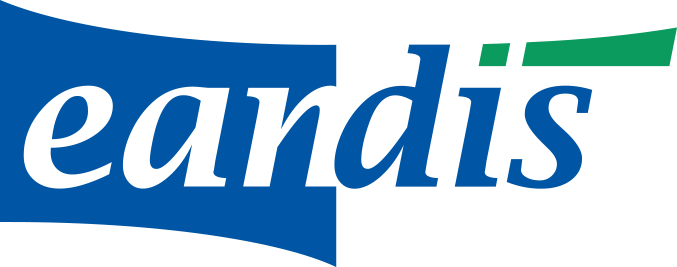
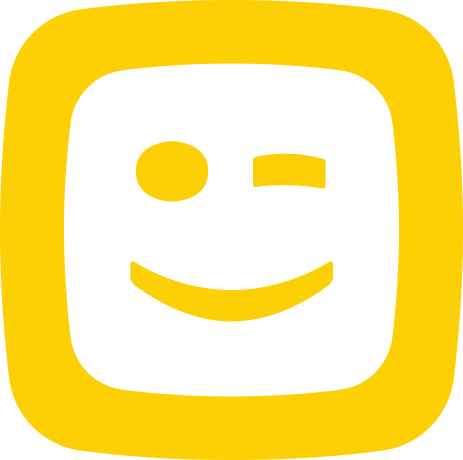
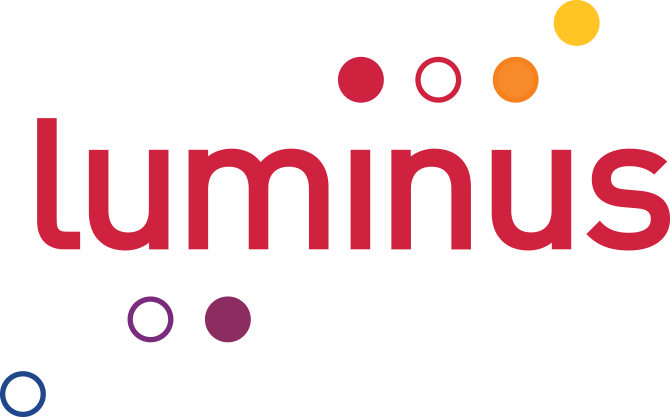
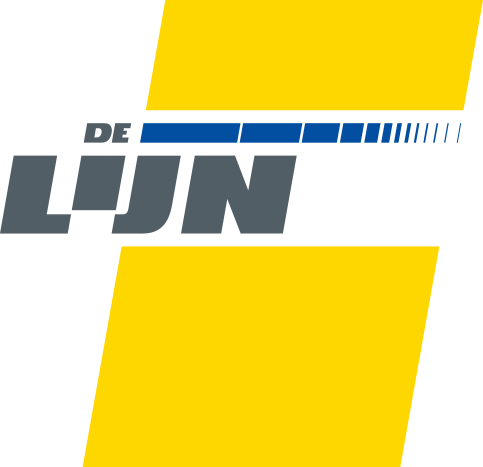
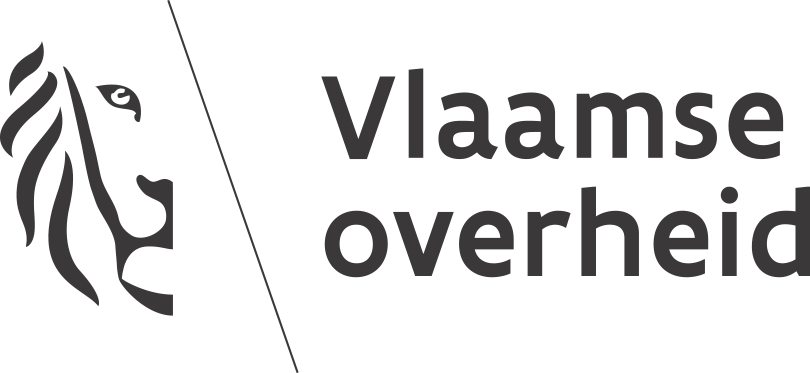
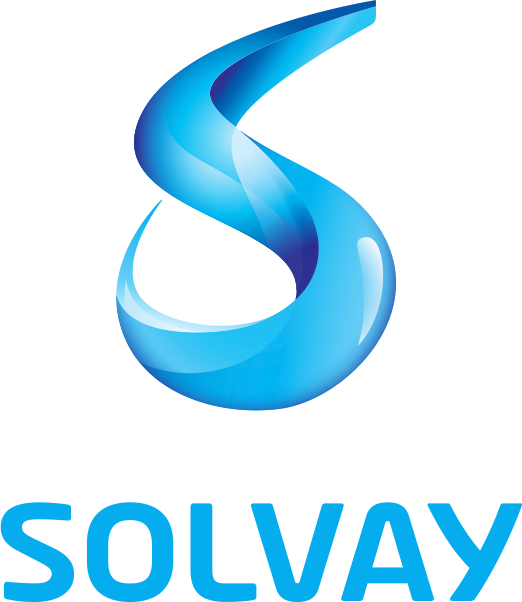
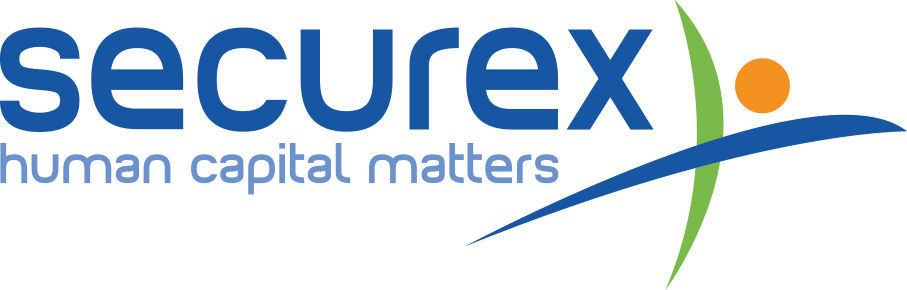
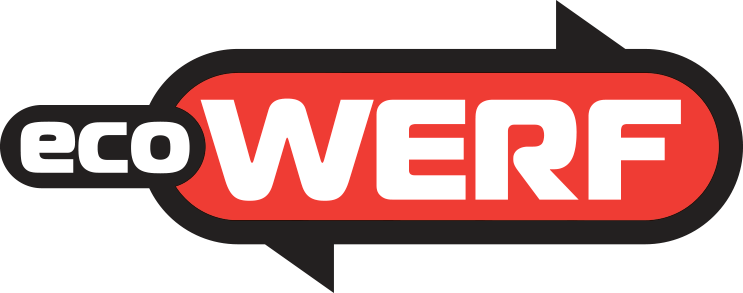
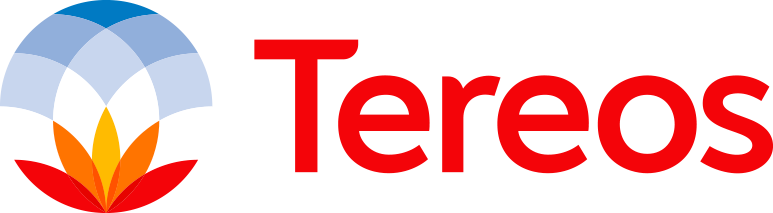
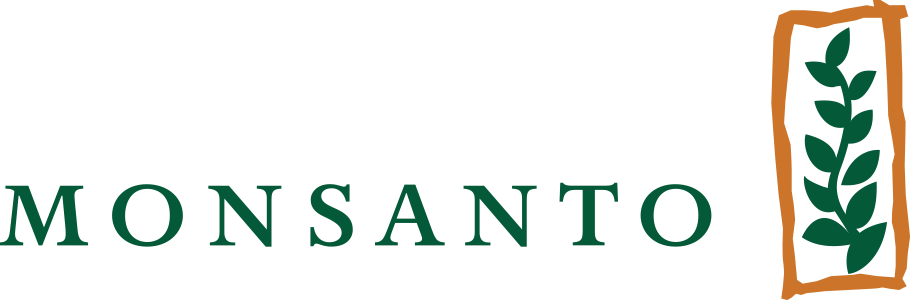
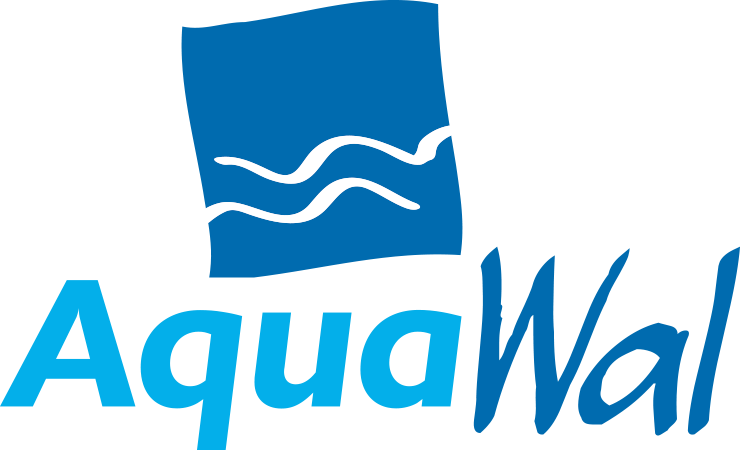
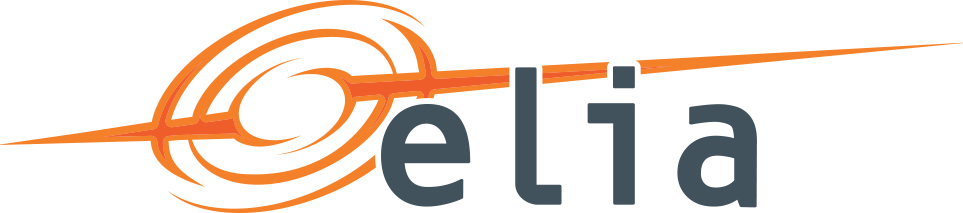
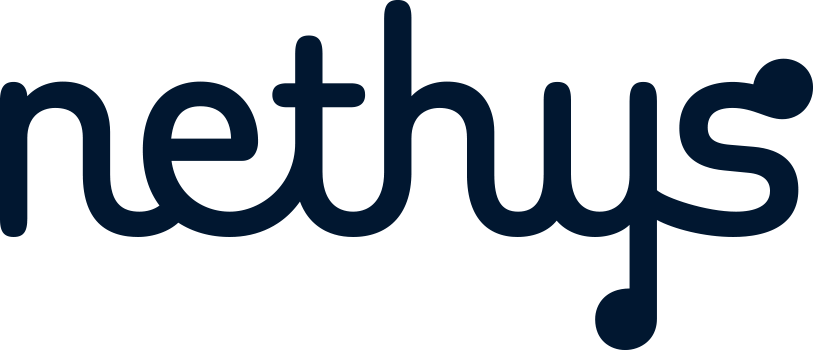
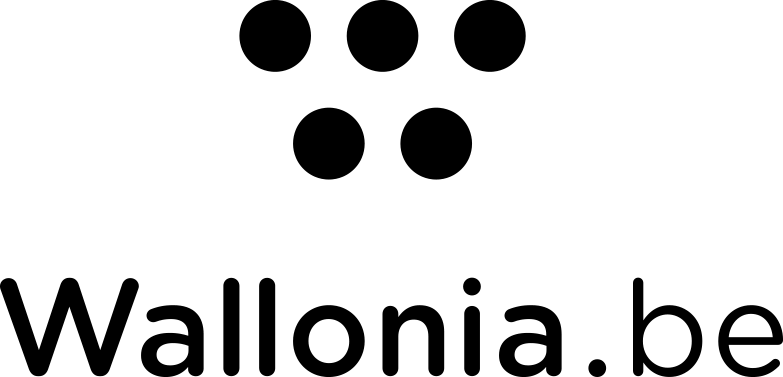
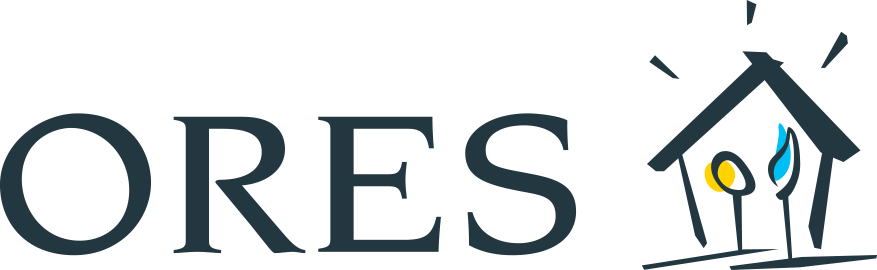
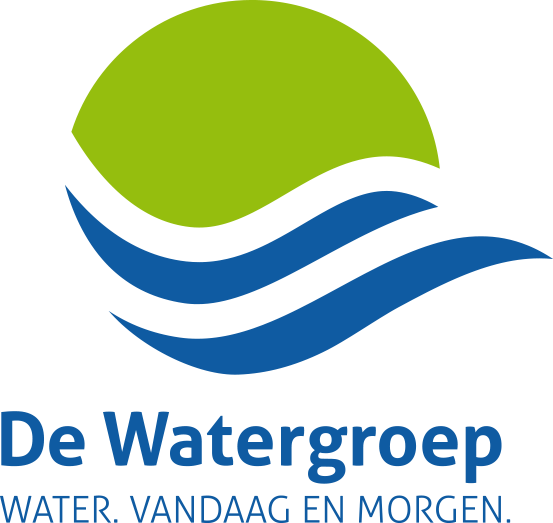
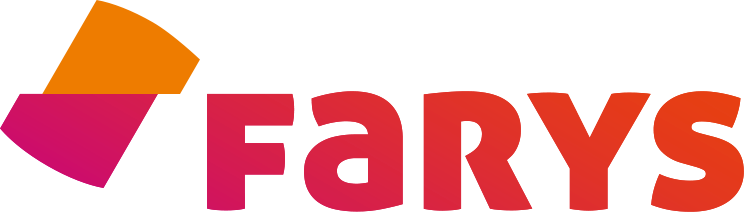
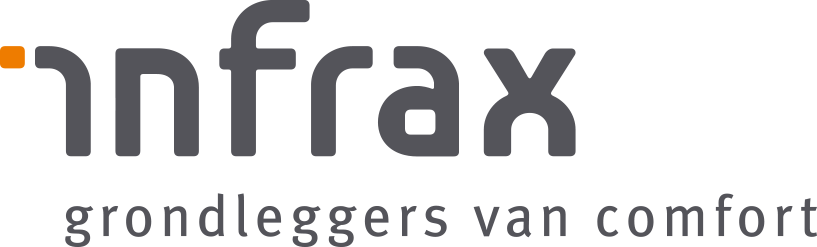
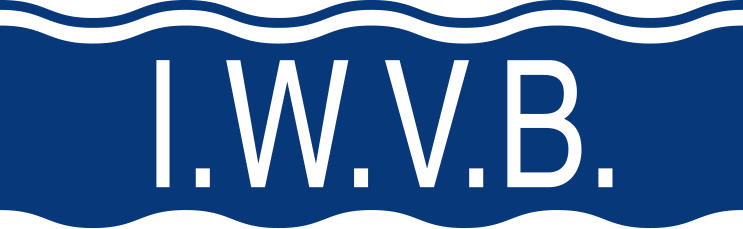

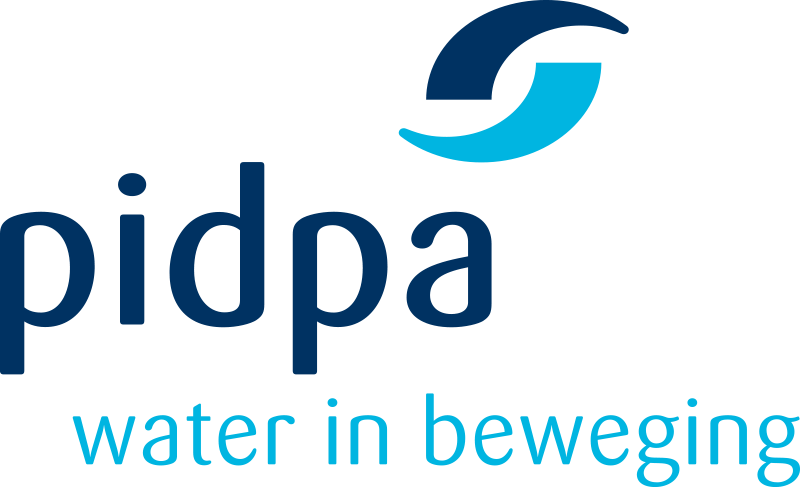